Dry transformers. Reliability and safety.
9 March 2008
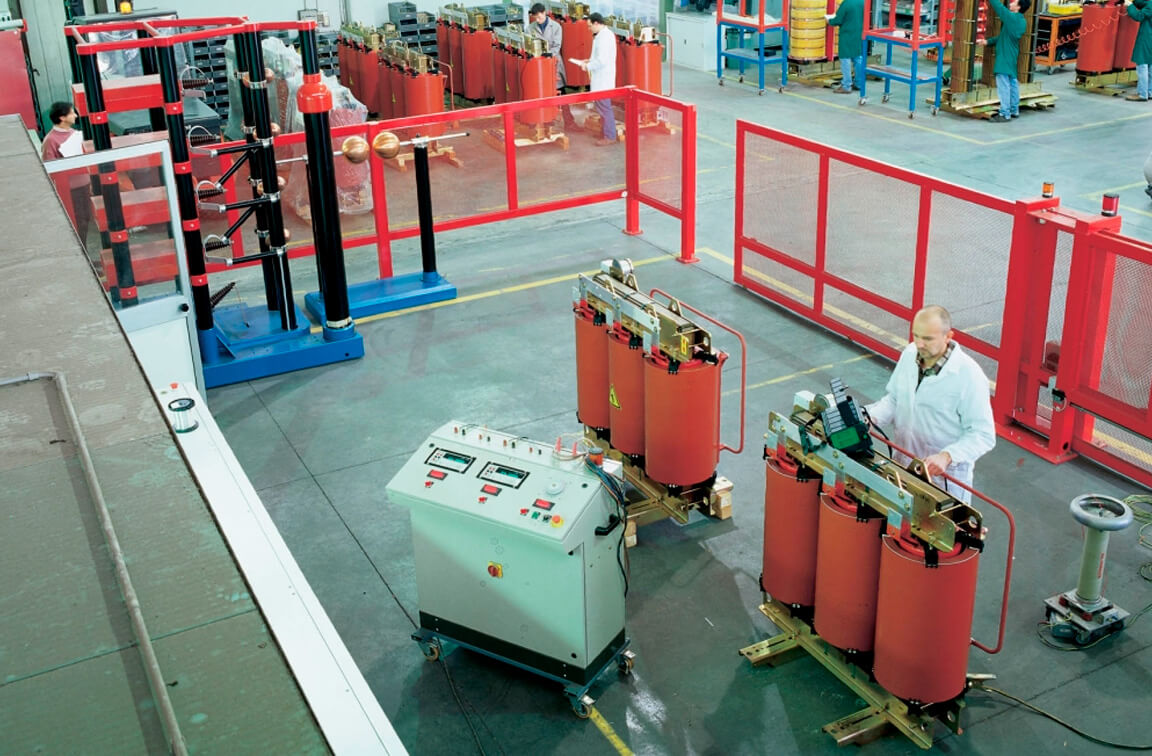
In Russia's modern competitive and efficient economy, the development of the energy sector is a priority. Among the diverse electrical equipment used in the transmission and distribution of energy, power transformers play a key role.
The main field of application of transformers is electric power facilities with their own complex of urban power grids, thermal power plants, hydroelectric power plants, GRES, nuclear power plants; industrial enterprises; mining, non-ferrous, ferrous metallurgy; oil and gas production and processing industries, as well as railways.
The power supply of such a huge number of facilities requires an extensive network of transformer substations. At the same time, each industry has its own plans for the construction of new and reconstruction of existing ones. All this is actively stimulating the transformer equipment market and, as a result, the number of different types and brands of transformers offered is increasing.
In the conditions of modern operation, strict requirements are imposed on the transformer as the main element of the substation. Moreover, both the basic technical characteristics and environmental friendliness (the absence of toxic emissions from accidents in substations, spillage of insulating liquid).
In Russia, oil transformers are installed and are being installed at most facilities. In most cases, this is due to their relatively low cost. However, oil transformers have a number of serious disadvantages, such as fire hazard and environmental risk of oil leakage. In addition, there is a constant need to monitor the oil level and quality. This, of course, complicates their operation and does not allow the use of oil transformers at facilities located as close as possible to consumers. Also, their weight and overall dimensions exceed dry transformers of similar power.
The rapid development of scientific progress and increased safety standards in the operation of high—voltage equipment made it possible to put into operation another type of equipment - dry transformers.
If we talk about the features of various design options and manufacturing technologies for dry transformers presented on the Russian market, then the most critical and responsible element of the dry transformer design, which determines its consumer properties, is high-voltage windings. Their quality depends on the materials used and the manufacturing technology.
Initially, dry transformers with windings made using monolith technology were widely used in Russia. This technology has proven itself quite well over the many years of its use. The electrical strength of the windings of dry transformers is ensured by the use of appropriate wire insulation. The mechanical strength of the structure is achieved through the use of bandages, which guarantee solidity after impregnation with varnishes and subsequent baking.
It should be noted that after impregnation, the electrical strength of the insulation decreases somewhat, but due to the separation of insulation functions and mechanical rigidity into different materials, this technology makes it possible to operate the equipment for a long time under cyclic thermal loads without reducing the electrical characteristics of the insulation.
In the manufacture of dry transformers with open windings, the insulating properties of the winding conductors made of fiberglass or nomex and solid insulating materials in the form of special pressed profiles are used. They give both mechanical rigidity to the structure and provide insulating properties of the transformer. When using insulating profiles and high-strength porcelain insulators, vertical and horizontal cooling channels are formed in the transformer structure, which effectively cools the windings.
Recently, dry transformers with cast winding have appeared on the Russian market. In them, the mechanical rigidity of the winding structure is ensured by the use of special fillers. It consists of epoxy resin with inert and flame-resistant fillers. In this case, the mixing and pouring process is carried out in a vacuum. This has significantly improved the mechanical, heat-conducting, and fire-fighting properties of cast-insulated transformers. This technology gives the windings high dielectric properties with an extremely low occurrence of partial discharges.
In addition, the cast winding makes it possible to obtain powerful dry transformers in small dimensions for use in networks with a higher voltage level.
Advantages of dry transformers are provided by new insulating materials, modern design principles and manufacturing technologies.
Currently, the dry transformer market in Russia is mainly represented by products from foreign manufacturers such as Schneider Electric, ABB, Siemens, GBE s.r.l, HTT, Bez Transformatory, etc.
The share of Russian manufacturers of such power equipment using modern technologies is significantly lower today. Although the opening of new production facilities and the constant expansion of the range within the same production by Russian market participants suggests a significant increase in the production of Russian dry transformers in the near future.