"Electronmash" JSC: Modern Electric Grid Infrastructure Needs Effective Technologies
3 December 2020
Source: Энергетика и промышленность России. Выпуск № 23 (403) ноябрь 2020 г.
Themes:
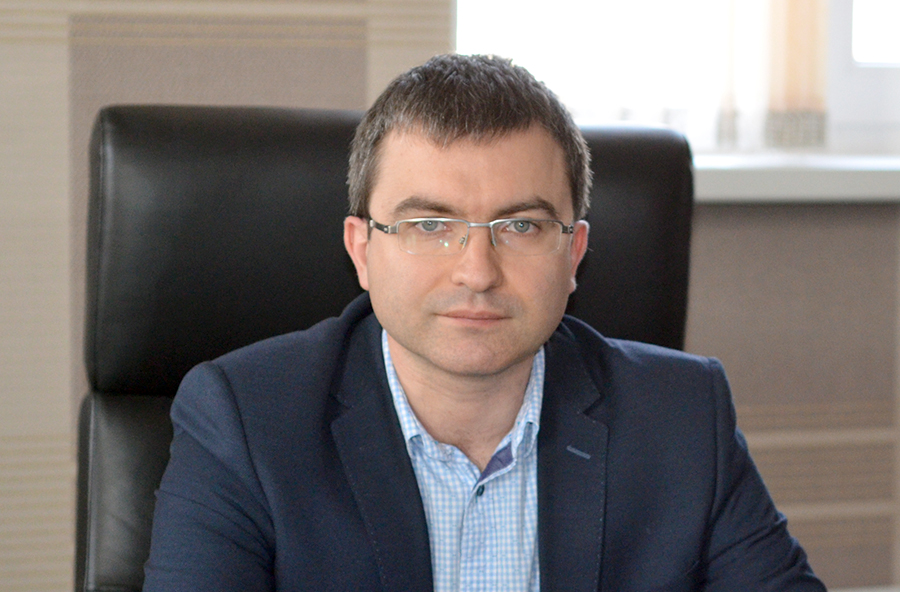
— Andrey Vladimirovich, the climatic conditions in Russia are very diverse—ranging from extremely low temperatures to tropical heat. At the same time, the sphere of state interests has shifted northward, into the area of extreme temperatures. Is this a challenge for manufacturers of electrical equipment in terms of its technical characteristics? Will harsh climatic conditions ultimately have a negative impact on the reliability of energy systems?
— Indeed, the adopted Strategy for the Development of the Arctic Zone of the Russian Federation and ensuring national security until 2035, as well as plans for the development of mineral resources in Eastern Siberia, indicate that in the current decade, some new electric grid facilities will operate in very cold climatic zones. As a manufacturer, we see this reflected in the number of projects we are implementing. Certainly, our country has a rich experience in operating under extreme climatic conditions. However, the time has come when our customers can afford to use new technical solutions that we and many other leaders in the electrical engineering market are now offering.
In my opinion, to ensure the reliable operation of network equipment in harsh climatic conditions, manufacturers must focus primarily on applying technical solutions that minimize the likelihood of so-called unstable failures. This type of failure is usually caused by random natural impacts and may cease on its own after the disconnection or change of operation mode of the network equipment. Unfortunately, extreme climatic conditions are quite unpredictable and can very likely negatively affect the reliability of electrical grid equipment, leading to a significant number of random failures. However, many random failures can be avoided by using specially designed structural solutions.
Thus, it is within the power of equipment manufacturers and consumers to minimize the impact of natural conditions by reducing the duration of exposure to adverse climatic conditions and the area of electrical grid facilities. For example, for substations rated 110-220 kV, this means implementing architectural, hardware, and layout solutions aimed at compactly placing all equipment whenever possible — except for power lines within quickly assembled modular buildings of high factory readiness.
We have the technologies for this; they have been tested and are applied, for instance, in the construction of electrical grid facilities in dense urban areas. Naturally, components with high element reliability should also be used, as the cost of a stable failure in northern conditions can be fatal. This approach will guarantee improved continuity of power supply metrics, such as SAIDI and SAIFI, by minimizing the impact of climatic conditions on electrical equipment.
Of course, the owners of electrical grid facilities — our industrial enterprises — will not be able to influence the reliability of the network beyond their balance sheet, but they will be confident that they have done everything necessary for uninterrupted power supply to their consumers in extreme climatic conditions.
— The implementation of large infrastructure projects and the development of new territories is inextricably linked to the development of the electric power industry. It is evident that the replacement of morally outdated equipment will proceed through retrofitting and modernization using the best available technologies or new construction. Which of these paths do you think is more feasible and in demand, and in what cases?
— When it comes to the networks of the unified national energy system, according to open statistics, the adopted programs for upgrading the electric grid complex have indeed significantly reduced the amount of outdated equipment and increased the reliability of power supply to consumers. However, most of our customers represent the mining and processing sectors of industry and are located on the other side of the balance sheet boundary. In this case, the choice between retrofitting and new construction is determined by the specifics of production and the "maturity" of the facility itself.
Logically, for already operating enterprises with continuous production cycles, the path of modernizing equipment and retrofitting, in the broadest sense of the word, is preferable. It allows for planned replacement of individual elements of the power supply system, transitioning to a repair scheme beforehand. After all, as a rule, they do not have new areas for this purpose. And if it is a deep input substation, they also have limited network maneuverability compared to the networks. Moreover, the time spent on this repair scheme is quite limited and sometimes involves partial shutdowns of technological processes, which also imposes special requirements on the technologies used for work and the equipment employed. Such facilities always require additional engineering developments from us to organize seamless phased integration of equipment.
The geography of new infrastructure projects and territories is such that newly created industrial facilities are usually built in open fields. In such cases, based on our experience, the vast majority of projects involve new network construction using the best available technologies. This is typically true for both the internal power supply system of the enterprise and the external network, provided there is a possibility for technological connection to the unified national energy system.
Retrofitting external networks is also usually impractical in most such cases, as it rarely meets the requirements for capacity and reliability for new powerful production facilities. Therefore, when deciding to start new construction, the customer tries to minimize their risks due to equipment failures.
The cost of unutilized electricity in the industrial sector is too high, and the payback period for infrastructure projects should not depend on the reliability of electrical grid equipment. In harsh natural conditions and with a strict project implementation schedule, new construction is often simpler and faster than retrofitting.
Of course, the reasons for choosing new construction over retrofitting in the development of new territories and infrastructure are numerous. However, the main point is that domestic manufacturers, including our company, which has accumulated significant experience in equipment development over its twenty years of existence, have much to offer to ensure reliable power supply for new facilities that meet all our customers' requirements.
— The exploration and development of new territories are associated with a high dynamics of electrical load growth. Construction of electrical networks does not always keep pace with the increasing demands of consumers. What principles should be embedded in electrical equipment to ensure an optimal scenario for network construction at new facilities?
— Indeed, if we look at the map, the geography of new projects from our customers determines the requirements not only for energy equipment but also for the overall dynamics of project implementation. Any investor is interested in commissioning a facility in the shortest possible time, constrained by natural conditions and the need for business optimization.
This becomes possible when most of the construction and installation works are carried out off-site, at our manufacturing plant, while only quick assembly of modules, comprehensive commissioning, and operational launch are done on-site. With this approach, even personnel training can take place during the control assembly of the equipment. Moreover, the technologies and production organization at "Electronmash" allow us to provide customers with direct access to the equipment during this period, along with specialized training programs, ensuring that personnel are prepared for the confident operation of the new facility by the time of completion.
As a result, the set of principles embedded in modern electrical equipment should include mobility, modularity, low maintenance, and high observability.
Mobility enables the transportation of individual modules, such as substation equipment, using standard road transport, with transfers to water transport and then over ice roads or even by helicopters.
Modularity allows us to quickly assemble individual modules and, using a wide network of modules, scale them by capacity or application features when necessary.
Low maintenance implies a reduction in the need for constant servicing personnel and fewer service visits due to advanced diagnostic tools, which lowers operational costs. At the same time, observability and manageability of such substations become paramount.
Regarding the optimal scenario for network construction, I believe it should also ensure high project development dynamics. Rarely does a customer expect a ready technological connection at 110 kV by the start of construction. Therefore, in practice, they begin with the construction of their distributed generation. Only then do they consider the feasibility and possibility of connecting to the ENES, as the ENES is, de facto, a more "inertial" component in this process.
As manufacturers we also adhere to the aforementioned principles in the production of our equipment to ensure a high development dynamic for the customer's project. Our approach to equipment design not only helps to put the facility into operation on time but also optimizes ownership costs, increases reliability, and helps achieve many other benefits that are obvious to our customers.
— An important issue in any electricity project during its justification phase is the minimization of capital and operating expenses without compromising the quality and reliability of power supply. At first glance, reducing one may increase the other, and vice versa. Is it possible to simultaneously reduce these costs? What qualities should electrical network equipment possess to minimize these expenses?
— Capital and operating expenses are undoubtedly significant parameters during the technical and economic justification of our customers' projects. Initially, reducing the area of the energy facility leads to an increase in its cost. On the other hand, a smaller facility typically requires less maintenance. It seems sufficient to find the intersection point of the graphs of these two dependencies to obtain a solution with the lowest capital and operating expenses.
However, looking more broadly, the question of minimizing CAPEX and OPEX is not entirely correct. In my view, it is unwise to make quick conclusions at the project feasibility stage based solely on capital and operating costs to choose a particular solution. It is essential to find an optimal ratio of these expenses that will lead to the best financial results.
In other words, CAPEX and OPEX are merely two variables of a more complex objective function, the essence of which is to maximize net present income over a fixed planning period. Equipment with the optimal set of parameters, selected based on the results of this function's calculations, should lead the investor to the shortest payback period.
Methodologically, we can approach this as an optimization problem, establishing empirical dependencies of CAPEX and OPEX on the area of the energy facility, boundary conditions, and other parameters, resulting in the determination of the optimal composition of equipment, CAPEX, and OPEX. A simpler practical calculation approach is iterative, where for various CAPEX and OPEX calculated for a set of existing hardware, architectural, and layout solutions for the energy facility, the net present income is sequentially determined until its maximum value is reached.
In our collaboration with customers on projects, we employ both methodologies for selecting the parameters of the proposed technical solution. However, the key takeaway remains that the solution must possess optimal, rather than minimal, CAPEX and OPEX, which will ultimately lead to the shortest payback period for the project.
From a climatic perspective, our experience suggests that the optimal solution is often a compromise suitable for moderate climate conditions, while energy facilities operating in extreme conditions tend to have a high ratio of capital costs to operational costs. In technical terms, this means that in northern regions, compact equipment must be utilized, despite the availability of larger spaces, to construct reliable, rapidly deployable, low-maintenance energy facilities with high observability.
— The energy system is a living organism, aimed at ensuring reliable power supply to consumers. What modern technologies available in the electrical engineering industry can be most effectively applied to further enhance reliability, and why?
— The continuity of electricity production and consumption processes, along with their unpredictability, makes the energy system truly dynamic, with the ultimate goal of providing reliable power to consumers.
It is well-known that both large and small power systems, including those of industrial enterprises, regularly face challenges such as weak links, power shortages, high electricity costs, and reduced reliability.
In this context, both consumers and electricity suppliers are striving to implement modern technologies available today. We observe these trends in the technical solutions of our clients as we collaborate on pilot innovative projects.
Some are moving towards establishing additional generation sources, while others are using automation and digital technologies to enhance network reliability. Some are even exploring unconventional technologies, such as additional generation from renewable sources and the use of network energy storage for various purposes.
Thus, I would like to highlight two readily available technologies for achieving reliability enhancement goals that our customers have already begun to test in various forms: the use of distributed generation and distributed intelligent management systems.
Having distributed generation in close proximity to local consumers significantly reduces dependence on centralized networks and ensures quick and independent access to energy resources. It also allows for better management of one's resources in a way that reduces overall economic costs for increasing connected capacity, which is particularly important for new projects.
It is worth noting that distributed generation, combined with the use of energy storage systems, is currently viewed as a crucial component of global energy development trends. In this trend, the application of intelligent distributed management systems and energy storage solutions addresses issues of instantaneous imbalances.
This opens up opportunities to ensure the stable operation of distributed generation, improve the efficiency of solar or wind stations, reduce the fuel component in electricity costs, and free up capacity in electrical network equipment.
Each of these methods for constructing distributed systems and employing energy storage solutions should lead to improved reliability of power supply and enhance project payback.
That’s why "Electronmash" places significant emphasis on engineering solutions and the preparation of technical and economic justifications, where we calculate optimal parameters for distributed systems and their components, as well as scenarios for their application tied to specific projects. This enables the customer to achieve the expected benefits from the technology.