«Электронмаш»: курс на инновации
19 февраля 2018
Источник: Энергетика и промышленность России. Выпуск № (306) ноябрь 2016 г.
Темы:
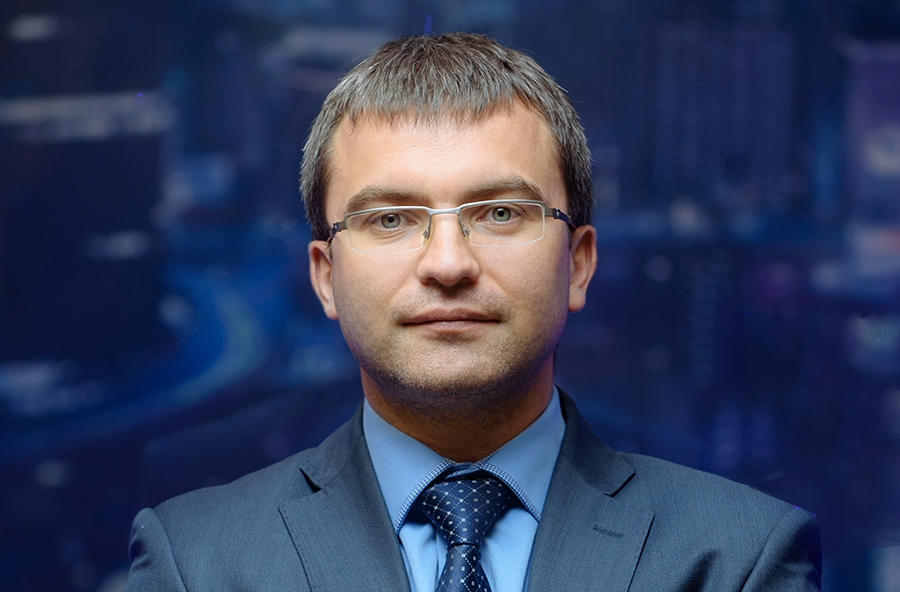
– Какова ситуация с импортозамещением в сфере оборудования для электрических сетей?
– На рынке российского оборудования релейной защиты, автоматизации и телекоммуникации, а также измерительных приборов и приборов учета присутствует достаточное количество современных решений. Силовое оборудование напряжением 6‑110 кВ также представлено российскими производителями с высочайшим качеством продукции. Так что мы как завод – изготовитель оборудования КРУ 6‑35 кВ и КТП 6‑35‑110 кВ не испытываем проблем с российскими комплектующими. Однако, как ни странно, в части силового оборудования 0,4 кВ полноценные конкурентные решения отсутствуют. Впечатление, что оборудование 0,4 кВ по определению простое, весьма обманчиво. Полноценная линейка силового коммутационного оборудования 0,4 кВ должна соответствовать высоким требованиям к его весовым, габаритным, эксплуатационным и функциональным характеристикам. Современные тенденции в производстве данного оборудования подразумевают увеличение надежности, уменьшение габаритов при сохранении нагрузочной и коммутационной способности, расширение требований к наблюдаемости объектов и возможностям телеуправления, новые функциональные требования в контексте развития автоматизированных систем управления и повышения энергоэффективности в рамках концепций «умной энергетики» и «умной технологии». Таким образом, силовое коммутационное оборудование 0,4 кВ – это отдельная, сложная, наукоемкая область. Силовое коммутационное оборудование 0,4 кВ, производимое в России, сегодня уступает импортному по номенклатуре и номинальным параметрам. Практически ни один российский производитель данного оборудования не предлагает полноценных линеек, обеспечивающих замещение продуктов мировых лидеров (ABB,Schneider Electric, Siemens).
– Сложившаяся ситуация отражается на вас как на заводе – изготовителе электрощитовой продукции 0,4 кВ?
– Отражается. Прежде всего – невозможностью полноценного импортозамещения комплектующих ввиду отсутствия линеек оборудования требуемых исполнений и характеристик, для которых была бы предусмотрена номенклатура аксессуаров, обеспечивающих ту самую «умную энергетику» и «умную технологию» и реализованных на базе современных надежных решений. Безусловно, наш завод заинтересован в разработке решений, построенных на базе оборудования отечественного производства для обеспечения конкурентного предложения на рынке электротехнической продукции. С этой целью мы постоянно анализируем российское оборудование в контексте обеспечения требований, выдвигаемых нашими крупными корпоративными заказчиками, такими, как «Газпром», «Газпромнефть», «Лукойл» и другими, проводим специальное тестирование оборудования совместно с заказчиками и собираем статистику опытной эксплуатации. И специалисты нашей компании, и наши заказчики отмечают, что при всей экономической привлекательности российского коммутационного оборудования 0,4 кВ уровень его качества и функциональности заметно уступает продукции международных лидеров отрасли.
– Может быть, сложившаяся ситуация требует привлечения импортных компаний к созданию совместных предприятий? Насколько велика роль российской стороны в этом процессе? Видите ли вы возможность создания СП с высокой степенью локализациипродукции,то есть отличных от «отверточных» производств?
– Российская сторона сейчас не особо может влиять на создание полноценных СП. И это, скорее, вопрос интереса иностранных производителей к сохранению и расширению объема российского рынка. При наличии заинтересованности импортных компаний локализация производства импортного оборудования в России возможна. Фактически это предполагает создание производств под конкретные линейки продуктов под управлением международной компании – именно таким путем развивался Китай. Теоретически это возможно, если, например, международная компания выкупит российское профильное предприятие либо организует новое, на зарегистрированном в РФ дочернем предприятии, и запустит на его мощностях производство своей продукции из отечественных материалов, но по своей технологии. В ином случае локализация останется на уровне «отверточной сборки». Собственно, это мы сейчас наблюдаем на ряде примеров, когда под видом отечественного оборудования предлагаются перелицованные аппараты азиатского происхождения или аппараты, собираемые из импортных комплектующих. Также велика вероятность локализации производства преимущественно устаревших, бюджетных аппаратов с урезанным функционалом или бытовых линеек оборудования. Такая ситуация связана в том числе и с нежеланием международных компаний передавать свои инженерные разработки и технологии, составляющие ключевую компетенцию, конкурентам и аутсорсерам, что обусловлено сетевой организационной структурой производства. Для локализации производства международных компаний в России должны быть приняты политические решения в виде налоговых льгот, субсидий на запуск производства, повышения налоговых ввозных пошлин на конкурентнуюпродукцию.
– Что мешает российским предприятиям, специализирующимся на производстве силового коммутационного оборудования 0,4 кВ,предлагать конкурентные решения?
– Мешает высокая стоимость разработки и освоения такого производства. Это вызвано большим объемом требуемых испытаний, объемом опытно‑конструкторских разработок и затратами на станки и оборудование. Высокие первоначальные затраты обусловлены долгим периодом отсутствия развития в отрасли производства силового коммутационного оборудования 0,4 кВ и сопутствующим отставанием в профильных областях, таких, как электротехническое материаловедение, микроэлектроника и другие. Ярко выражена нехватка квалифицированного инженерного персонала в этой области. Проблема усугубляется вопросами патентования, так как основные эффективные технические решения уже запатентованы международными производителями, вследствие чего российские разработчики вынуждены тратить значительные ресурсы на поиск альтернативных решений.
– Иными словами, планы российских властей довести путем импортозамещения и локализации долю отечественной продукции до 90 процентов утопичны?
– Эти планы в настоящее время не имеют под собой материальной базы. Ужесточение требований к проценту использования российского и локализованного оборудования в составе готовых изделий, очевидно, приведет к спаду объема рынка ключевых международных производителей. Однако следует понимать, что при этом произойдет падение качества и уменьшение функциональности конечной продукции. Без дополнительных мер по поддержке собственного производства и обеспечения заинтересованности импортных компаний в организации местных производств ужесточение требований не приведет к реальному импортозамещению. В настоящий момент очевидно, что с учетом всех перечисленных проблем процесс импортозамещения в области силового коммутационного оборудования 0,4 кВ займет длительное время и потребует существенных затрат ресурсов от всех заинтересованных сторон.
– В этом году принято решение о создании Национальной ассоциации испытательных центров на базе Федерального испытательного центра«Россетей».Что, на ваш взгляд,эта мера даст российским производителям?
– «Электронмаш» как крупный производитель электротехнического оборудования, имеющий существенный опыт поставки оборудования как для российского рынка и стран СНГ, так и для международного рынка, понимая важность этого проекта, в первую очередь заинтересован в создании Национальной ассоциации испытательных центров на базе Федерального испытательного центра «Россетей». На сегодняшний день при осуществлении поставок на зарубежные рынки мы вынуждены проводить дополнительные процедуры сертификации оборудования в стране назначения или в международных центрах сертификации, так как на настоящий момент действие внутренних российских протоколов испытаний, к сожалению, не признается за рубежом. Такие затраты ложатся на стоимость конечной продукции, тем самым снижая нашу конкурентоспособность при поставке оборудования на международные рынки. Заявленная деятельность национальной ассоциации испытательных центров совместно с Техническим комитетом по стандартизации «Электроэнергетика» (ТК‑016) в направлении оптимизации и гармонизации параметров и требований к электрооборудованию с мировыми требованиями позволит нам выполнять поставки оборудования не только на внутренние рынки, но и расширить работу с международными EPC-контракторами, использующими наше оборудование при реализации ответственных проектов
на территории России, а также рассматривающими применение нашей продукции на внешних рынках.
– Поможет ли такая ассоциация решить проблему собственной и импортной продукции сомнительного происхождения и низкого качества?
– Мы надеемся, что национальная ассоциация в достаточно короткие сроки сможет выработать общие «прозрачные» требования и методику проверки изделий, что позволит проводить единые испытания на соответствие отечественным и зарубежным требованиям (ГОСТ Р, IEC, IEEE, GB). Однако все вышесказанное будет иметь успех, если национальная ассоциация испытательных центров обеспечит выполнение единых требований всеми испытательными центрами, входящими в ассоциацию, и при этом будет жестко контролировать эти стандарты качества. Такая деятельность поможет решить проблему российской и импортной продукции сомнительного происхождения и низкого качества, обезопасив нашу энергетику от оборудования, не соответствующего заявленным требованиям. В конечном итоге весь этот комплекс мер будет способствовать повышению уровня отечественной энергетики.
– В последнее время энергетикисталкиваютсяс частымисюрпризами природы – циклонами, тайфунами, ледяными дождями и прочим. Какие решения, позволяющие защитить сетевые объекты от природных катаклизмов,предлагает ваша компания?
– Нам хорошо знакома работа в суровых климатических условиях: существенная часть наших заказчиков – это компании электросетевых предприятий и нефтегазового сектора, объекты которых расположены в северных широтах Западной и Восточной Сибири и Дальнего Востока. Поэтому наша компания уделяет большое внимание разработке технических решений, позволяющих защитить сетевые объекты и оперативно – эксплуатационный персонал, работающий на них, от природных катаклизмов, ну или хотя бы существенно снизить их влияние.
Для работы в таких условиях мы разработали серию комплектных трансформаторных подстанций КТП‑ELM‑35/10 (6) кВ, отказавшись от традиционных подстанционных решений с открытыми распределительными устройствами (ОРУ) на напряжение 35 кВ, сделав выбор в пользу подстанций с закрытыми распределительными устройствами (ЗРУ), позволяющими снизить воздействия природных факторов либо полностью их избежать. Закрытые распределительные устройства (ЗРУ) 35 кВ и 10 (6) кВ от АО «Электронмаш» – это быстромонтируемое блочно‑модульное здание высокой степени заводской готовности, укомплектованное комплектными распределительными устройствами (КРУ) «Элтима» и «Элтима +» со всеми необходимыми системами жизнеобеспечения: отоплением, освещением, вентиляцией, пожароохранной сигнализацией и другими, необходимыми по требованиям заказчика.
Они выдерживают сейсмическую активность до 9 баллов включительно по шкале MSK, защищают оборудование от осадков, ветровой и снеговой нагрузки, позволяют эксплуатировать их при температурах от –60 °С. Все наши модификации КРУ, используемые для производства КТП 35/10 (6) кВ, имеют в своей производственной линейке полностью моторизованные модификации, могут быть оборудованы системой внутреннего видеонаблюдения за положением заземлителя и кассетно‑выдвижного элемента с выключателем, а также системой контроля температуры контактных соединений шин. В составе релейного отсека предусмотрена установка не только МП РЗА, но и комплекта распределенной системы управления ячейкой: контроллер присоединения, обеспечивающий управление выключателем, приводом КВЭ и заземлителя, собирающий основные состояния КРУ, обеспечивающий необходимые блокировки и передачу данных в систему ТМ (АСУ ТП) КТП.
Таким образом, полное соответствие производимых нами КТП требованиям к подстанциям нового поколения обеспечивает главную цель создания подстанций нового поколения – значительное уменьшение объема эксплуатационного и ремонтного обслуживания, оперативное управление с удаленного диспетчерского пункта и центра обслуживания сетей, переход к работе без постоянного обслуживающего персонала, планированию и проведению ремонтов по фактическому состоянию оборудования. Изготавливаемые нами подстанции, помимо соответствия всем техническим регламентам наших заказчиков, полностью обеспечивают выполнение стандартов Системного оператора ЕЭС в части проведения переключений в электроустановках. В таком решении коммутационное оборудование: измерительные трансформаторы, ОПН, шинная система и остальное оборудование, размещены внутри шкафов КРУ и надежно защищены от всех внешних природных воздействий, не только стойким к механическим и коррозионным воздействиям корпусом шкафа КРУ, но и самим зданием ЗРУ. Таким образом, эксплуатация оборудования, оснащенного всеми современными цифровыми системами, осуществляется в комфортных условиях отапливаемого помещения – переключения подводятся дистанционно по каналам оперативно диспетчерского управления без выезда персонала на объект. Это и есть те наши решения, которые мы выдвигаем для защиты сетевых объектов от природных катаклизмов.
– Одно из ключевых «энергетических» решений осени 2016 года – утверждение дорожной карты «умной» энергетики. Насколько значимо это решение как для электросетевогокомплекса РФ, так и для производителей, разработчиков, имеющих шансы участвовать в этом проекте?
– Безусловно, наличие такой дорожной карты и, в принципе, такой инициативы со стороны правительства Российской Федерации – это очень важное решение не только для электросетевого комплекса РФ, но и для нас – производителей современного российского электротехнического оборудования. Министерство энергетики РФ в дорожной карте EnergyNet в рамках Национальной технологической инициативы предусматривает создание цифровых электроэнергетических сетей; со своей стороны мы как завод – производитель оборудования, имеющий в своем портфолио оборудование, необходимое для функционирования таких энергообъектов, получим возможность поставлять такое оборудование, а не только обсуждать и разрабатывать его. В настоящий момент наш потребитель смотрит на разработки в области цифровых подстанций скорее как на концепт светлого будущего, а с утверждением дорожной карты будут определены и сроки, и методы конкретных внедрений, разработаны документы национальной системы стандартизации и прочие нормативно‑технические акты в области функционирования комплексных систем и сервисов «умной» энергетики. В рамках развития «умной» энергетики в настоящее время мы прорабатываем комплексные решения для цифровых подстанций и цифровых сетей среднего и низкого напряжения, энергетической инфраструктуры промышленных предприятий, разрабатываем электротехническое оборудование для применения в составе объектов генерации, функционирующих на возобновляемых источниках энергии. В настоящее время мы приступили к производству оборудования в рамках строительства ветряной электрической станции 35 МВт в Ульяновской области, активно ведем инжиниринговые проработки по нескольким объектам солнечной генерации.
– Как вы считаете, оправдаются ли ожидания руководства отрасли,связанные с этими планами?
– Покажет время. Но те технические инновации, которые уже работают в отрасли, как говорят наши заказчики, это всерьез и надолго. К этой инициативе отрасль шла давно и последовательно. Первые признаки мы увидели в документах ОАО «ФСК ЕЭС» в январе 2004 года, когда были сформированы «Общие технические требования к подстанциям 330‑750 кВ нового поколения». Понимание необходимости технических инноваций и принципов их применения впоследствии было отражено в «Единой технической политике Россетей» в 2013 году и в дальнейшем нашло свое логическое продолжение в рамках Национальной технологической инициативы. Мы внимательно отслеживаем все инновационные требования и пожелания наших клиентов и уделяем большое внимание совершенствованию своего оборудования и технических решений. Тем самым мы обеспечиваем электротехническое оборудование высокими эксплуатационными характеристиками, соответствующими требованиям не только сегодняшнего, но и завтрашнего дня.
– Какие проблемы сетевых компаний может решить «умная» энергетика?
– По нашему мнению, цифровая электроэнергетическая сеть, предлагаемая к внедрению в рамках НТИ и состоящая из интеллектуальных коммутационных аппаратов, систем управления и учета энергии, оперативно‑диспетчерского управления, позволит сетевым компаниям снизить стоимость владения сетью, уменьшить потери в ней, снизить аварийность и сроки восстановления после технологических инцидентов. Внедрение распределенной генерации, потребителей с управляемой нагрузкой и накопителем электроэнергии позволит сократить расходы на создание и поддержание работоспособности резервов.